Industry 4.0: Smaller Indian firms need policy boost to catch up
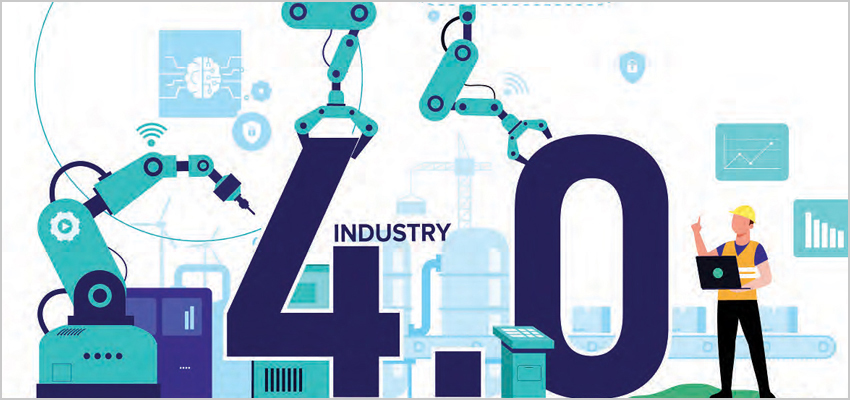
Scale and skill two major challenges for MSMEs
The world is now experiencing a fourth industrial revolution that can revolutionise the Indian market, but we need to ensure smaller enterprises don’t get left behind.
Manufacturing industries experienced incremental and radical advancements in operations at various levels from the 17th to 20th century across the globe. Earlier, advancements happened in procurement, process, production, distribution and feedback and collectively improved the operational efficiencies of industries.
Today, Industry 4.0 encompasses implementing big data, robotics, the internet of things (IoT), artificial intelligence, machine learning and cloud services for automation and autonomous operations in industries.
The need for it arises primarily due to increasing demand and market competition.
India is an emerging and one of the fastest-growing economies. So, it experiences increasing demands due to ballooning population and market competition due to globalisation and privatisation.
It is pertinent for the Indian industry to embrace the advancements in manufacturing operations to cater to the demand-driven economy and sustain the external market competition.
There are several policies to encourage the adoption of Industry 4.0 across manufacturing sectors in India. Smart manufacturing centres are formed across the country, like one at Centre for Product Design and Manufacturing at Indian Institute of Science, Karnataka.
This echoes the ambitious objective to increase the Gross Domestic Product contribution of manufacturing from the existing 16 per cent to 25 per cent by 2025.
Indian companies may enhance their operating profit by 40 per cent and reduce the planned capital expenditure by 10 per cent just by adopting Industries 4.0, according to management consulting firm McKinsey & Company.
Indeed, there are numerous benefits of adopting Industry 4.0 for the manufacturing industries. However, the key lies in its implementation, given the limitations and challenges Indian industries have. The country is still at a nascent stage of Industry 4.0 adoption and will take time and effort to transform the industry fully.
Industry 4.0 prescribes the systematic adoption of advanced technologies and processes. These sophisticated technologies require significant capital expenditure and skilled labour for operation.
The challenges of capital requirement and skilled labour are teething more in the Indian manufacturing sector, given the significant presence of Micro, Small and Medium Enterprises (MSME). Although MSMEs contribute significantly to overall manufacturing output, export and employment in the nation, they are equally constrained by capital and skilled labour.
MSMEs typically operate as a captive industry and specific component supplier to a large industry and thus do not enjoy the benefits of economies of scale. This is one of the major reasons that hinder MSMEs from capital investments in advanced technologies and subsequent automation and expansion.
Thus, the absence of economies of scale and lack of skilled labour pose a challenge to India’s MSMEs for Industry 4.0 adoption. We further discuss these two significant bottlenecks - scale and skill - and their consequences in the Indian industries in the following sections.
"Policy support must be provided to manufacturing firms, especially to MSMEs, to incentivise investments in modernisation and to upskill the workforce. It will foster the Indian industry to join the Industry 4.0 club and become globally competent."
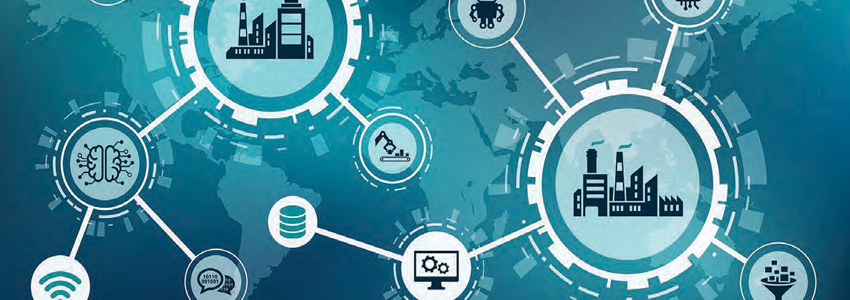
Policy help for scale challenges
Economies of scale are the cost advantages companies experience when the overall cost of production can be spread over a larger output.
A small manufacturing firm with limited investment size, market and output does not enjoy such benefit of economies of scale. MSMEs primarily operate on a narrow margin that restricts them from investing in advanced and sophisticated technologies, which are the pillars of Industry 4.0.
This restricts the growth of MSMEs. In contrast, large-scale manufacturing firms that enjoy the benefits of economies of scale have the leverage to experiment and implement Industry 4.0. This further boosts the firms’ productivity and, thereby, profit margin.
A high-profit margin may again translate into technological upgradation and modernisation. Hence, a virtuous cycle of investment and growth runs in the case of large firms that may turn larger over a period with the implementation of Industry 4.0.
Whereas MSMEs with a limited opportunity for investment and technological advancement lag in implementing Industry 4.0.
Over time, the gap between MSMEs and large-scale firms may increase, which will affect the overall production and employment in the economy. Hence, it is necessary to provide policy support primarily to MSMEs to adopt Industry 4.0 through healthier investments.
Labour upskilling to handle skill needs
Apart from capital, skilled labour is essential for implementing Industry 4.0, which requires sophisticated machinery and automated systems. The advanced techniques need skilled labour to operate them.
There are two challenges pertaining to skilled labour: Availability and affordability. There is a scarcity of skilled labour to implement and operate advanced machinery and systems. If there is availability in some instances, the issue is with their affordability.
Recruitment of skilled labour by an MSME firm inflates the operating cost and poses an operational challenge to the firm’s sustainability. Hence, not just the capital investment but also the skilled labour engagement is the constraint for MSMEs when they go for upgradation, sophistication and automation.
However, there is a silver lining when we talk about skilled labour. Upskilling existing labour through academic collaboration, apprenticeship and industrial training may aid industries in addressing the issue of skilled labour.
At large, the shift of the workforce from low-skill (manual) jobs to high-skill (automation) jobs increases the overall productivity of the industries. This implies that labour upskilling, as part of Industry 4.0 implementation, brings enhanced productivity and efficiency to the industry.
Labour upskilling may hedge better margins and, thus, scope for further investments in modernisation. In other words, the industry may enter a virtuous cycle of upskilling, modernisation and expansion in the long run.
In sum, we have discussed the two dimensions of Industry 4.0 implementation in Indian industry, especially in the context of MSMEs: Scale and skill. Lack of scale and skill in MSMEs restricts Indian manufacturing industries from investing, modernising and thereby adopting Industry 4.0.
Policy support must be provided to manufacturing firms, especially to MSMEs, to incentivise investments in modernisation and to upskill the workforce. It will foster the Indian industry to join the Industry 4.0 club and become globally competent.